In today’s world, getting accurate pressure readings is key in many fields. This is true for industries like industrial control and HVAC. The digital pressure gauge is a game-changer, making pressure measurement more precise and efficient. It uses the latest technology to help professionals make better decisions and improve their work.
Digital pressure gauges are great for monitoring pressure. They work with different sensors like bourdon tubes and piezoresistive sensors. These gauges show pressure readings clearly, making it easier to understand without mistakes. They are perfect for checking pressure in many areas, from industrial settings to HVAC systems.
Read interesting things at : grenzgamer
Key Takeaways
- Digital pressure gauges offer advanced measurement solutions for precise pressure monitoring across industries.
- These innovative devices leverage cutting-edge technology to deliver accurate, reliable, and efficient pressure readings.
- Digital pressure gauges integrate with various sensor technologies, including bourdon tubes and capacitive pressure sensors.
- They provide clear and intuitive pressure displays, reducing the risk of manual interpretation errors.
- Digital pressure gauges are versatile tools that can be used in a wide range of applications, from industrial processes to HVAC systems.
Introduction to Digital Pressure Gauges
Digital pressure gauges are a big step forward in measuring pressure. They use electronic sensors and advanced digital processing. This makes them more accurate than old analog gauges.
Understanding Pressure Measurement Principles
Pressure is about the force on a surface area. It’s key in many fields, like making things and working with HVAC systems. Pressure measurement principles use special sensors to turn force into an electrical signal. This signal is then processed and shown on the gauge.
Benefits of Digital Pressure Gauges
Digital pressure gauges have many perks over analog ones:
- Enhanced Precision: They are more accurate and consistent, perfect for precise measurements.
- Improved Data Collection: They work well with data logging systems, making it easy to collect and analyze data.
- Easier Monitoring and Control: Their digital displays and features make it simple to watch and adjust pressure levels in real-time.
These advantages of digital pressure gauges have made them popular in many industries, including process control and HVAC systems.
Feature | Analog Pressure Gauge | Digital Pressure Gauge |
---|---|---|
Precision | Limited | Enhanced |
Data Collection | Manual | Automated |
Monitoring and Control | Challenging | Simplified |
Types of Digital Pressure Gauges
The world of digital pressure gauges is full of variety. They offer solutions for many industries. These tools give precise and reliable pressure readings, fitting many needs. Let’s look at the main types and what they can do.
Absolute Pressure Gauges
Absolute pressure gauges measure pressure against a perfect vacuum. This makes their readings not depend on air pressure. They’re great for places where absolute pressure matters, like in science, space, and advanced making.
Differential Pressure Gauges
Differential pressure gauges show the pressure difference between two points. They’re key in places where this difference is crucial, like in filters, flow, and control systems.
Vacuum Pressure Gauges
Vacuum pressure gauges measure low pressure or vacuum. They’re used in HVAC, refrigeration, and making semiconductors. These types of digital pressure gauges help control vacuum processes well.
Type of Digital Pressure Gauge | Key Applications |
---|---|
Absolute Pressure Gauge | Scientific research, aerospace, advanced manufacturing |
Differential Pressure Gauge | Filter monitoring, flow measurement, process control |
Vacuum Pressure Gauge | HVAC systems, refrigeration, semiconductor manufacturing |
Digital pressure gauges serve many industries, offering precision and flexibility. Knowing the types of digital pressure gauges and their uses helps professionals choose the best for their systems.
Working Principle of Digital Pressure Transducers
A digital pressure gauge has a key part called the pressure transducer. It turns pressure into an electrical signal. This signal is then processed digitally and shown on the gauge, giving accurate readings.
There are two main types of pressure transducers used: the Bourdon tube mechanism and capacitive pressure sensors.
Bourdon Tube Mechanism
The Bourdon tube mechanism is a well-known technology. It uses a coiled, curved tube filled with pressure medium. When pressure goes up, the tube straightens, sending an electrical signal.
This mechanism is strong and can handle high pressures. It’s often used in industrial settings.
Capacitive Pressure Sensors
Capacitive pressure sensors work differently. They use the idea of changing capacitance to measure pressure. The sensors have two conductive plates and a dielectric material between them.
When pressure is applied, the plates move closer or farther apart. This changes the capacitance. The change is then turned into an electrical signal, showing the pressure digitally.
These sensors are known for their high sensitivity and quick response. They’re great for many pressure measurement tasks, including those needing digital pressure transducer technology.
Knowing how these pressure transducer technologies work helps users choose the right digital pressure gauge for their needs.
Applications of Digital Pressure Gauges
Digital pressure gauges are used in many fields. They help in manufacturing, monitoring industrial processes, and in HVAC and refrigeration systems. These tools are key to improving efficiency and ensuring safety in many areas.
Industrial Process Monitoring
In the manufacturing world, digital pressure gauges are very important. They give accurate pressure readings in real-time. This helps operators spot problems, improve equipment, and keep things running smoothly.
They are used in many areas like chemical processing and food production. These gauges help keep the quality of products high.
HVAC and Refrigeration Systems
In HVAC and refrigeration, digital pressure gauges are crucial. They check the pressure of refrigerants and air. This helps technicians find leaks and make sure systems work well.
By doing this, they save energy, make equipment last longer, and avoid expensive repairs.
Industry | Application | Key Benefits |
---|---|---|
Industrial Process Monitoring | Monitoring and controlling critical processes | Optimized performance, enhanced quality, and process integrity |
HVAC and Refrigeration Systems | Monitoring refrigerant and air pressures | Improved energy efficiency, extended equipment lifespan, and reliable operation |
Digital pressure gauges are vital in many industries. They help with precise pressure monitoring. This is key for good performance, safety, and saving money. They are used in many areas, from controlling industrial processes to HVAC and refrigeration systems.
Factors to Consider When Choosing a Digital Pressure Gauge
Choosing the right digital pressure gauge is important. You need to think about accuracy, resolution, pressure range, and how it fits with your environment. Also, consider what kind of connection it needs. This ensures the gauge works well for your needs.
Accuracy and Resolution Matter: The gauge’s accuracy and resolution are key. If you need very precise measurements, look for a gauge with high accuracy and fine resolution. For less precise needs, you can find more affordable options.
Pressure Range: The gauge’s pressure range must match your application’s needs. It’s important to pick a gauge that can handle the pressure your application requires. This way, you get accurate and useful readings.
Pressure Range | Typical Applications |
---|---|
Low Pressure (0-100 psi) | HVAC systems, air compressors, medical equipment |
Medium Pressure (100-5,000 psi) | Industrial processes, hydraulic systems, pneumatic equipment |
High Pressure (5,000-20,000 psi) | Petrochemical operations, oil and gas exploration, advanced manufacturing |
Environmental Compatibility: The gauge must handle your environment well. This includes temperature, humidity, and any corrosive substances or vibrations it might face.
Connectivity Options: Today’s gauges offer many ways to connect, like digital interfaces and wireless protocols. Choose a gauge that fits your system’s needs. This makes it easier to monitor and integrate with your setup.
By thinking about these factors, you can find the best digital pressure gauge for your needs. This ensures you get accurate and reliable pressure measurements.
Accuracy and Precision of Digital Pressure Gauges
Accuracy and precision are key in pressure measurement. Digital pressure gauges aim to give reliable readings. But, they need regular calibration and care to keep working well.
Calibration and Maintenance Practices
Calibration is vital for digital pressure gauges. It checks if the gauge’s readings match a known standard. This ensures the gauge’s measurements are accurate, helping in making good decisions.
Keeping the gauges in good shape is also important. This means cleaning them, checking for damage, and replacing parts when needed. Following the maker’s advice helps the gauges last longer and work better.
Factors Affecting Accuracy | Factors Affecting Precision |
---|---|
|
|
Knowing how to improve accuracy and precision in digital pressure gauges is key. This ensures reliable measurements and better decision-making in many fields.
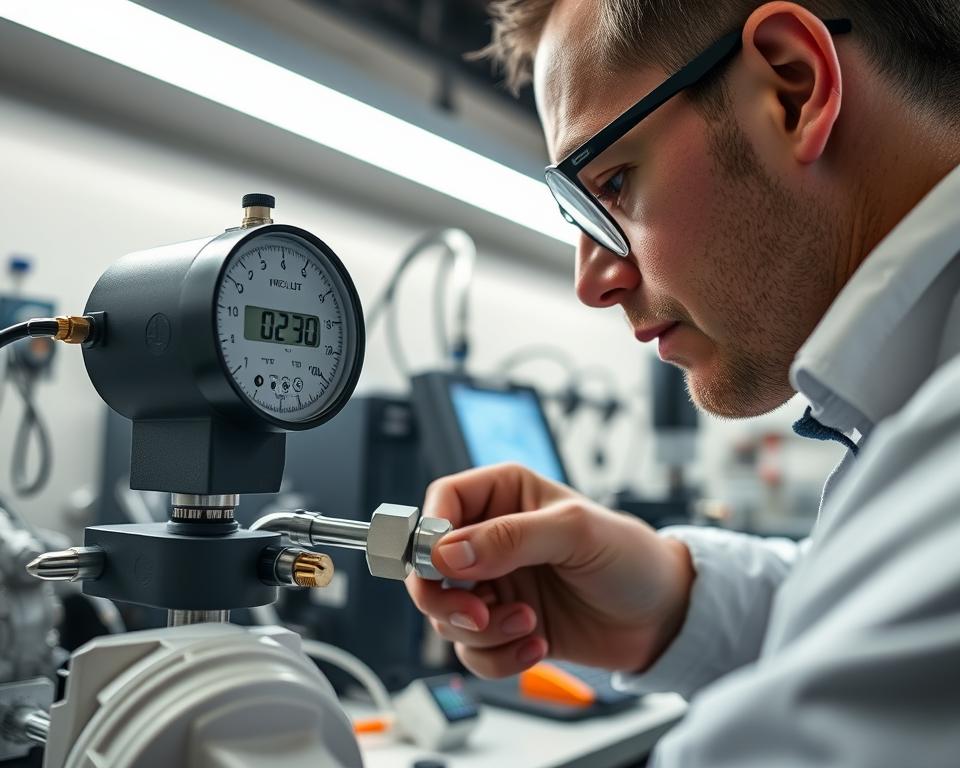
“Maintaining the accuracy and precision of digital pressure gauges is essential for reliable data collection and informed decision-making.”
Digital Pressure Gauge for Remote Monitoring
Digital pressure gauges let you watch pressure from afar. This is great when you can’t get to the spot easily or safely. They have wireless tech, log data, and work with big systems for easy monitoring.
With remote pressure monitoring, you can see important pressure info from anywhere. This helps you make quick decisions and fix problems fast. It makes things safer, more efficient, and better for your equipment and processes.
- Wireless connectivity: Digital pressure gauges with built-in wireless communication protocols, such as Wi-Fi or Bluetooth, enable real-time data transmission to a central monitoring system or mobile devices.
- Data logging: Advanced digital pressure gauges feature data logging functionality, allowing for the storage and retrieval of historical pressure data for analysis and reporting purposes.
- Integration with centralized monitoring: Seamless integration of digital pressure gauges with centralized control and monitoring systems, such as SCADA or Building Management Systems, empowers operators to track and manage pressure conditions across multiple locations from a single interface.
Digital pressure gauges with remote pressure monitoring are changing how we watch and manage pressure. They make things safer, more efficient, and better for your equipment and processes.
“Remote pressure monitoring with digital gauges has been a game-changer for our operations. It allows us to maintain tight control over critical pressure points from a central location, improving our responsiveness and overall process reliability.”
– John Smith, Maintenance Manager, XYZ Manufacturing
Integration with IoT and Industry 4.0
Digital pressure gauges are key in the Industry 4.0 and Internet of Things (IoT) era. They help create smart systems that use real-time data and predictive analytics. This leads to better efficiency and smarter decisions in many fields.
Smart Pressure Monitoring Systems
The use of iot pressure gauge tech with IoT and Industry 4.0 is changing how we monitor pressure. Smart systems with digital gauges send out pressure data in real-time. This allows for:
- Predictive maintenance: Spotting problems early with ongoing monitoring and analytics.
- Automated control: Adjusting pressure settings automatically for better efficiency and less manual work.
- Improved decision-making: Giving insights to improve production, maintenance, and resource use.
By adding smart pressure monitoring systems to their operations, companies can fully use Industry 4.0 and IoT. This boosts productivity, cuts downtime, and keeps pressure at the best levels in their processes.
Feature | Benefit |
---|---|
Real-time Pressure Monitoring | Sees pressure changes right away, allowing for quick action. |
Predictive Maintenance | Foresees and fixes pressure issues before they cause trouble. |
Automated Pressure Control | Improves efficiency by setting the best pressure levels automatically. |
Data-driven Decision Making | Uses pressure data for smarter choices and ongoing improvement. |
By using digital pressure gauges with IoT and Industry 4.0, companies can achieve more efficiency, save costs, and stay ahead in their field.
Environmental Considerations for Digital Pressure Gauges
Choosing the right digital pressure gauge is key. The environment it will work in matters a lot. These tools need to handle extreme temperatures, humidity, vibrations, and corrosive substances. Knowing what the environment demands is vital for their performance in industrial settings.
Digital pressure gauges are built to last. They have strong construction, weatherproof casings, and special coatings. These protect them from moisture, dust, and chemicals. They also have shock-absorbing parts and tough materials to handle vibrations and impacts.
Temperature is another big factor. Top-notch digital pressure gauges use smart temperature control and materials. This keeps them accurate and stable, even in very cold or hot conditions.
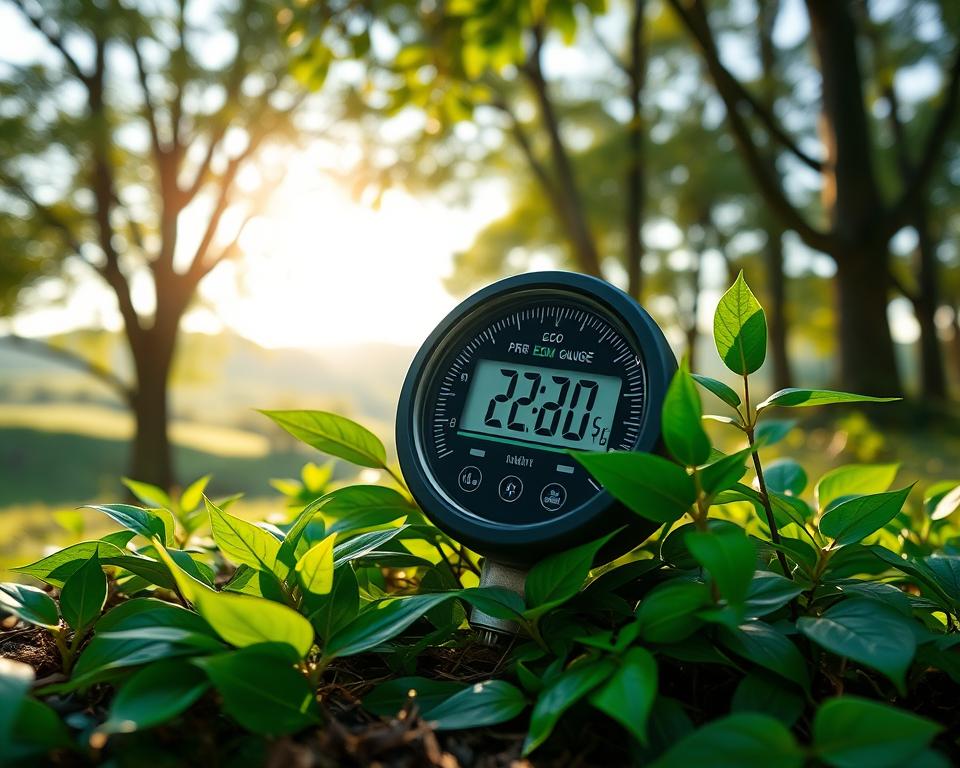
Manufacturers focus on these environmental aspects. This ensures digital pressure gauges work well and accurately, even in tough industrial settings. Paying attention to these factors is key to keeping pressure data reliable and supporting important industrial processes.
Differential Pressure Gauges and Vacuum Gauges
Digital pressure measurement has evolved with specialized tools like differential pressure gauges and vacuum gauges. These tools are key in various industries. They offer precise pressure readings in tough environments, solving complex measurement needs.
Specialized Applications
Differential pressure gauges measure pressure differences in systems. They’re used in HVAC, process control, and filter monitoring. These gauges spot small pressure changes, helping find system issues or blockages.
Vacuum gauges, on the other hand, measure low-pressure or vacuum conditions. They’re used in semiconductor making, labs, and vacuum processes. Keeping vacuum levels precise is vital for quality and performance.
Application | Differential Pressure Gauges | Vacuum Gauges |
---|---|---|
HVAC Systems | Monitoring pressure drop across filters, coils, and ducts | – |
Process Control | Detecting blockages, leaks, and flow issues in pipelines | – |
Semiconductor Manufacturing | – | Monitoring vacuum chambers and processes |
Laboratory Equipment | – | Ensuring proper vacuum levels for scientific experiments |
Using differential pressure gauges and vacuum gauges, professionals get accurate pressure readings. This helps them improve their work, keep things safe, and ensure quality.
Digital Pressure Gauge Manufacturers and Suppliers
The digital pressure gauge market has many manufacturers and suppliers. They offer a wide range of products for different industries. These companies lead in innovation, providing top-notch digital pressure gauge technologies.
Big names like Ashcroft, Wika, and Dwyer Instruments are at the top. They are known for quality, durability, and great customer support. They have digital pressure gauges for many industries, from process control to HVAC.
There are also specialized suppliers and smaller manufacturers in the market. They focus on specific needs, offering custom solutions and personal service. This meets the unique needs of their customers.
Manufacturer | Key Products | Unique Selling Points |
---|---|---|
Ashcroft |
|
|
Wika |
|
|
Dwyer Instruments |
|
|
These are just a few examples of the many digital pressure gauge manufacturers and suppliers. They offer a wide range of products and specialized expertise. This makes them well-suited to meet the growing demand for precise and reliable pressure measurement solutions across various industries.
Conclusion
Digital pressure gauges have changed how we measure and monitor pressure in many industries. These tools, like pressure transducers and manometers, offer precision and reliability. They help users improve their processes and make smarter decisions.
As the need for better pressure monitoring grows, digital gauges will be key. They support industrial automation and smart infrastructure. With features like remote monitoring and IoT integration, they boost efficiency and save costs.
Digital pressure gauges are essential in many fields, from manufacturing to oil and gas. Their ability to work in different settings and integrate with new tech makes them vital. As technology advances, so will the role of digital gauges in ensuring accurate pressure measurements.